Process Validation Solutions for Enhanced Structural Integrity
Addressing Aviation Maintenance Challenges with Process Validation
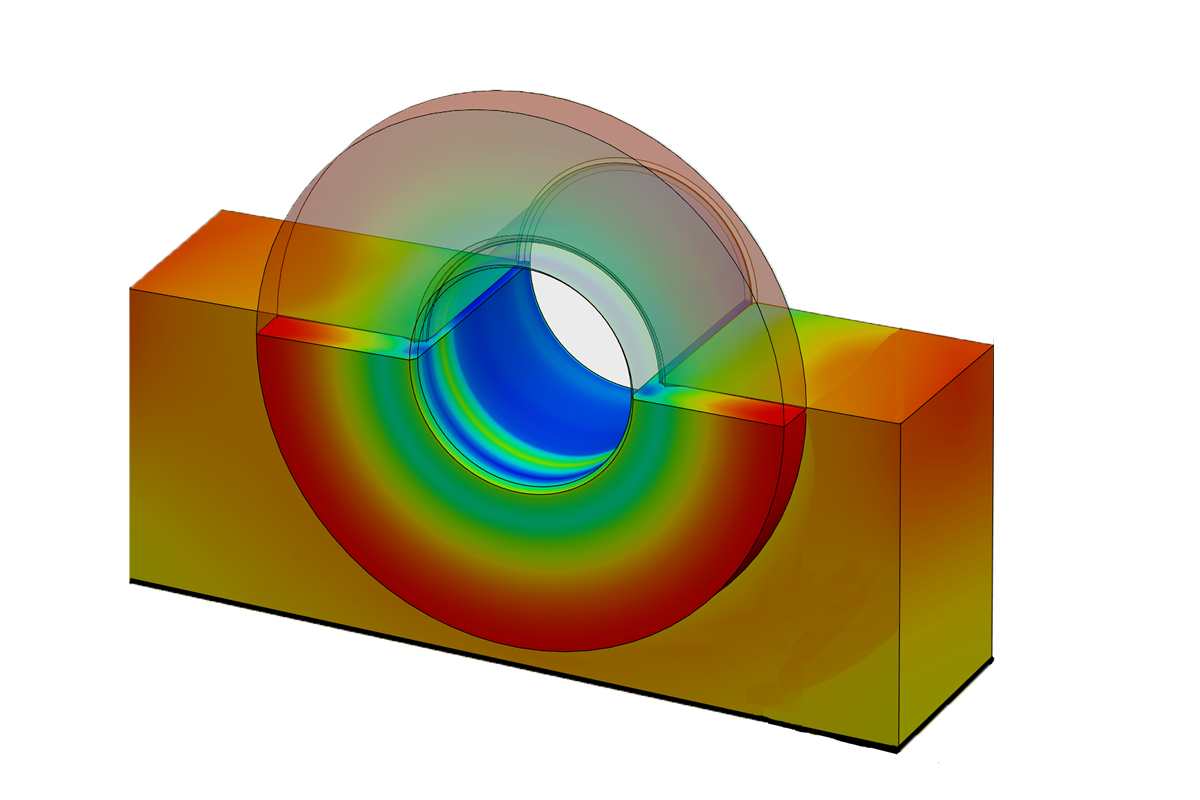
Engineered Residual Stress Solutions for Aviation
We work with customers to identify the critical product and process parameters to drive the design solution. This can include applied interference levels, minimum compression in the structure or not to exceed tensile stress limits. The designed configuration can be evaluated with analytical models, FEA, as well as experimental techniques including digital image correlation (DIC) and physical testing to ensure that the product and installation function as desired.
Handheld Smart Tools for Aircraft Cold Expansion Validation
PartWorks is leading innovation by developing the world’s first high-performance handheld cold expansion tool. This groundbreaking tool not only enhances cold expansion processes but also provides real-time validation. The handheld smart tool collects critical data from each repair, documenting the accuracy and quality of the expansion process.
Key Benefits of our cold expansion tool include:
- Fatigue test program integration: Validates that the cold expansion repair is performed correctly, preventing future structural failures.
- Life extension documentation: Each hole is carefully documented to support life extension credit for aircraft repair and aerospace maintenance.
- Portable and easy to use: Ideal for on-site repairs, enabling technicians to validate processes without needing to move the aircraft or structure to another location.
This process validation tool is essential for industries that require cold expansion repair validation to support aircraft life extension or critical component longevity.
Advanced In Situ Process Validation with Digital Image Correlation (DIC)
PartWorks is at the forefront of process validation technology with our patent-pending system for in-process validation of cold expansion. Utilizing digital image correlation (DIC), this in situ system offers unmatched precision in monitoring and validating the cold expansion process in real time. Our patent pending in situ process validation system is currently being developed for both standalone applications and as part of a fully integrated tool suite. This system provides both process validation and life extension support for critical repairs and structural enhancements, offering unparalleled accuracy and reliability.
Why Process Validation is Critical for Your Business
In industries such as aerospace, automotive, and industrial manufacturing, ensuring that components meet strict residual stress tolerances is critical to overall safety and performance. Process validation tools like those offered by PartWorks ensure that every repair is executed correctly, reducing the likelihood of structural failures, extending the life of critical components, and helping your business avoid costly downtime.
Request a Demo of PartWorks Process Validation Solutions
Explore how PartWorks’ process validation solutions can enhance your repair workflows and extend the life of your critical components. Request a demo today to see how our innovative tools, including residual stress solutions, handheld smart tools, and in-process validation systems, can transform your operations. Our team of experts is ready to collaborate with you to ensure the highest levels of process reliability and validation accuracy.
Explore the possibilities