Transforming Aircraft Maintenance, Repair, and Overhaul with PartWorks RepĀR™ Solutions
Solutions
The Maintenance, Repair, and Overhaul (MRO) industry faces constant challenges in reducing downtime, ensuring repair accuracy, and extending the service life of aircraft components. PartWorks RepĀR provides innovative solutions that leverage augmented reality (AR), computer vision, and cold expansion technologies to improve aircraft maintenance processes. By combining these advanced technologies with our Digital Twin integration and process validation tools, we help military and commercial aircraft operators enhance fleet readiness, minimize corrosion repair costs, and validate life extension credit.
Augmented Reality for Airframe Hole Repair, Fastener Installation and Inspection
With PartWorks RepĀR (patent pending), technicians can repair and inspect aircraft fastener holes faster and with greater accuracy than any legacy solution. By using a combination of augmented reality (AR), computer vision AI, and object tracking, PartWorks enables real-time data collection and improves the quality of MRO processes. The RepĀR system also contributes to the Digital Twin, providing an accurate, real-time digital representation of the aircraft that helps reduce errors, improve operational efficiency, and generate comprehensive multimedia documentation for future verification and training.
Benefits for MRO:
- Faster repair times with AR-guided instructions
- Greater accuracy in inspections and fastener hole repairs
- Seamless integration with the Digital Twin for enhanced process validation
- Real-time documentation for quality assurance and training purposes
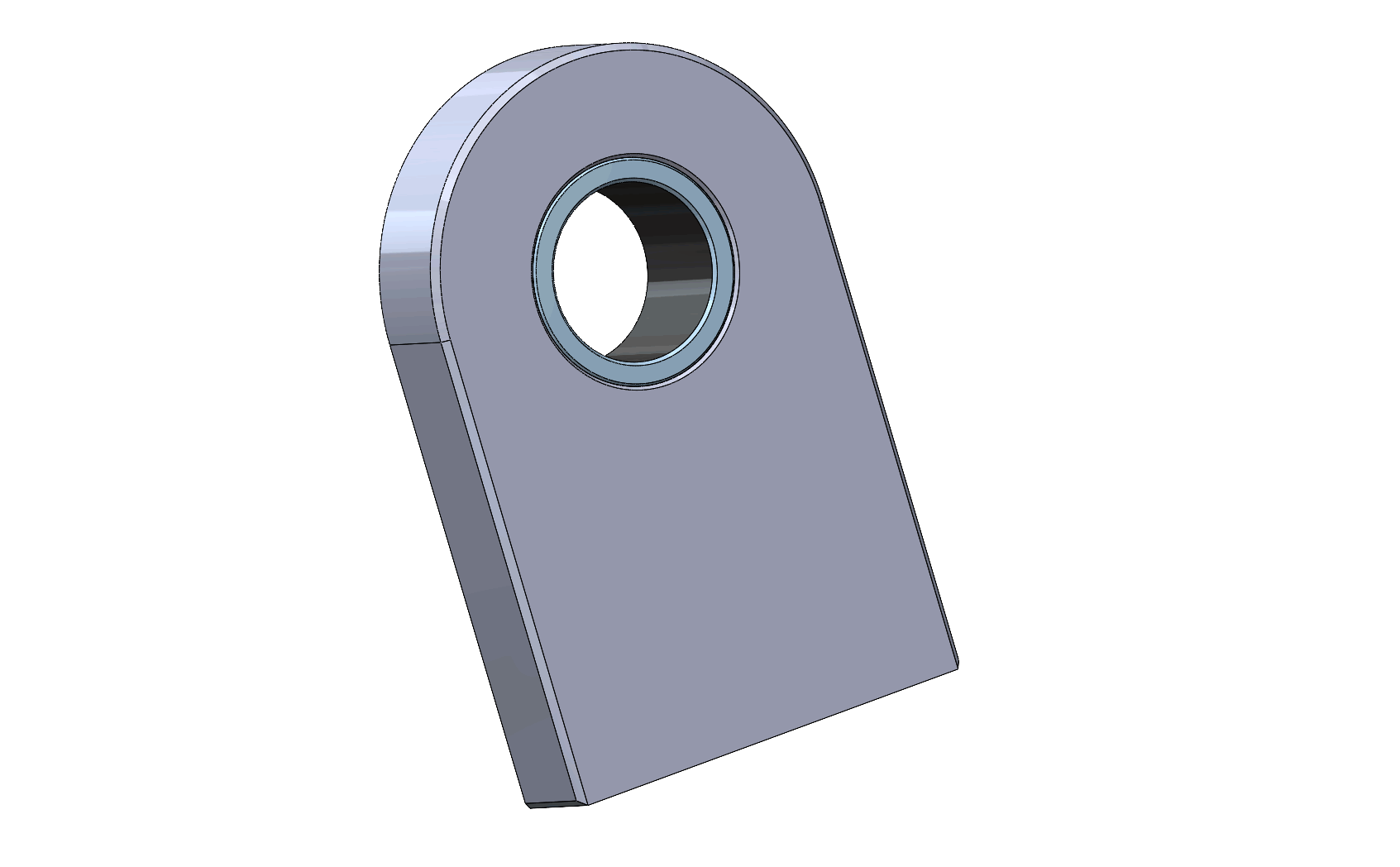
Expanded Bushings for Enhanced Structural Performance
PartWorks’ expanded fit journal bushings offer a high-performance solution that enhances both bushing and structural performance. Our cold expansion technology eliminates traditional installation processes that are prone to error, such as pressing or hammering, and avoids exposing workers to cryogenic materials. These custom bushing solutions are designed for general purpose manufacturing as well as for fatigue and damage tolerance enhancement. By working closely with customers, we validate these solutions through our analytical expertise and experimental testing.
Expanded bushings are available in all common aerospace materials, including Cres, Al-Ni-Bronze, and Titanium. Custom configurations, such as lubrication grooves and fluid ports, are designed to meet specific application needs, and the use of our hand-held hydraulic tool ensures fast, accurate installation.
Benefits for MRO:
- Enhanced bushing performance with minimal installation error
- Custom solutions validated for fatigue life extension
- Cold expansion techniques for improved structural integrity
- Available in a range of aerospace materials
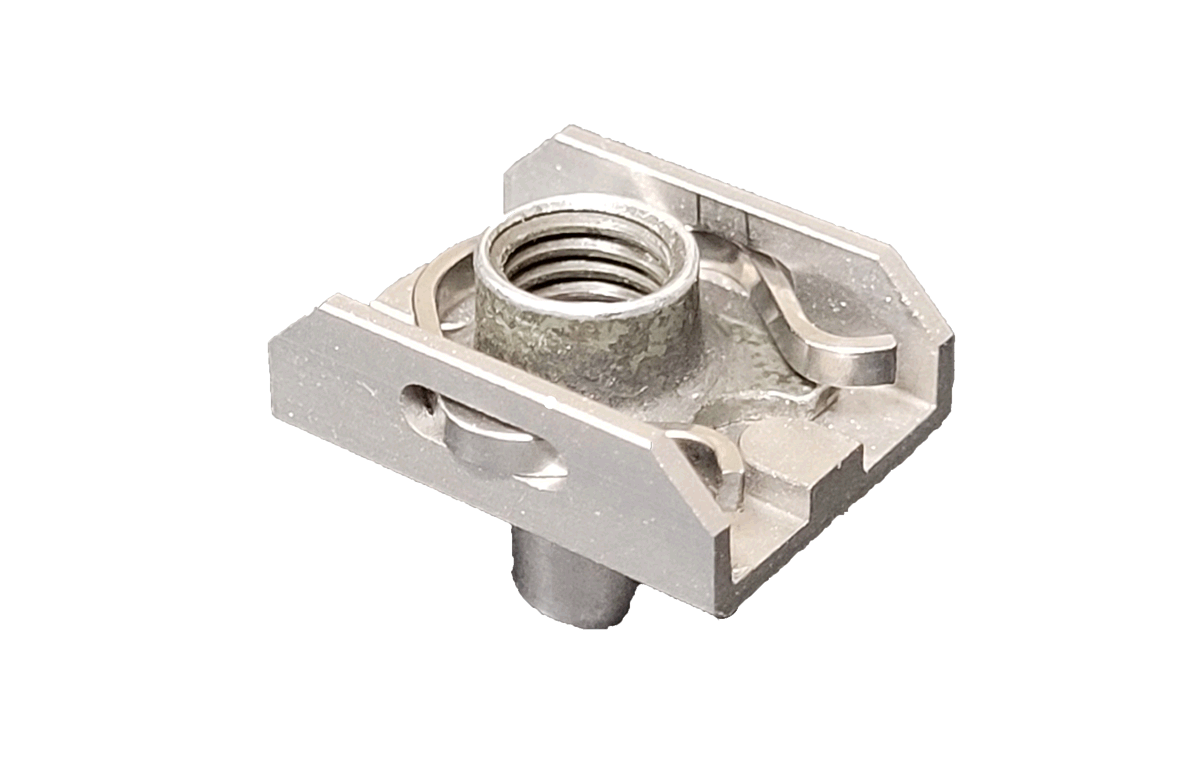
Ultra Thin-Walled Rivetless Nut Plates for Corrosion Repair
PartWorks’ bushed rivetless nut plates restore corroded holes to their original size with minimal material removal, maximizing the benefits of cold expansion and significantly extending the fatigue life of the component. Data from research sponsored by ONR and AFRL has demonstrated that our ultra thin-walled bushings offer life extension comparable to that of brand-new, uncorroded structures. By combining this technology with our patented adhesive repair method, we provide a long-term barrier against further corrosive damage.
This solution not only improves aircraft availability by reducing corrosion repair time, but also minimizes the need for costly part replacements.
Benefits for MRO:
- Life extension improvements comparable to new structures
- Corrosion hole repair with minimal material removal
- Long-term barrier against future corrosion damage
Reduced downtime and extended part life
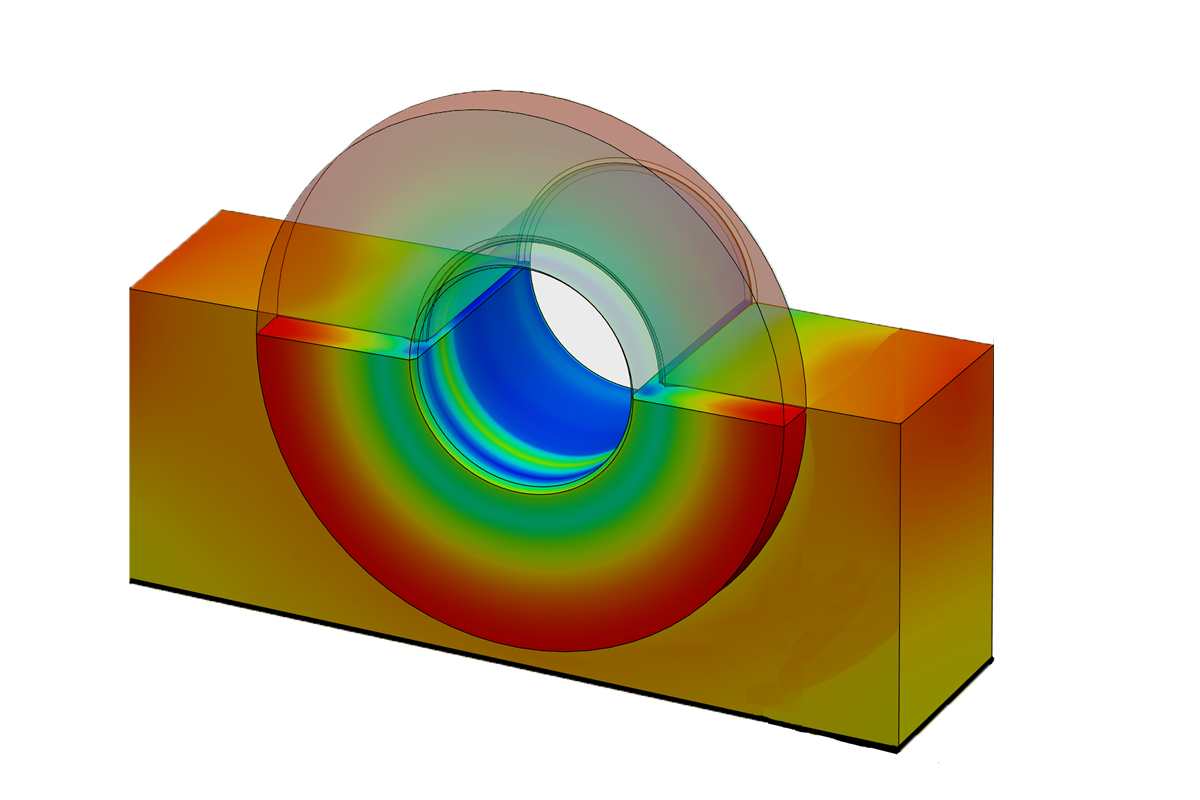
Engineered Residual Stress Solutions for Fatigue Enhancement
PartWorks’ engineered residual stress solutions are designed to enhance the fatigue life and damage tolerance of fastened structures and pinned joints. We collaborate with customers to determine the critical product and process parameters, including applied interference levels, minimum compression, and tensile stress limits. These configurations are validated through advanced evaluation techniques such as digital image correlation (DIC) and physical testing, ensuring that each product performs as required in the most demanding aviation maintenance environments.
Benefits for MRO:
- Enhanced fatigue life of fastened structures
- Solutions tailored to specific aviation maintenance needs
- Digital image correlation for real-time validation of repairs
- Improved damage tolerance of critical aircraft components
Handheld Smart Tools for Cold Expansion Process Validation
PartWorks is pioneering the world’s first AR-capable, high-performance handheld cold expansion tool. This tool collects real-time data from each repair to ensure that the cold expansion process is performed accurately. Using parameters derived from fatigue test programs, the tool validates each repair, documenting the process to support life extension credit for the aircraft.
By ensuring that each hole is repaired correctly, this handheld smart tool improves repair accuracy and provides the documentation necessary for quality control.
Benefits for MRO:
- Real-time validation of cold expansion processes
- Documentation that supports life extension credit
- Increased repair accuracy through AR-guided steps
- Easy-to-use, portable tool for fast, efficient repairs
Advanced In Situ Process Validation for Cold Expansion
PartWorks is developing a patent-pending system for in situ process validation of cold expansion using digital image correlation (DIC). This system allows technicians to validate repairs in real-time, ensuring that each cold expansion is performed to exacting standards. Available as both a standalone system and as part of an integrated tool, our solution provides accurate process validation that supports the case for life extension credit.
This capability allows MRO teams to confidently verify the integrity of repairs and ensure that critical components meet the necessary standards for long-term reliability.
Benefits for MRO:
- Real-time validation of cold expansion processes
- Accurate data for life extension credit
- Available as a standalone or integrated solution
- Supports compliance with aviation maintenance standards
By integrating PartWorks RepĀR into MRO operations, military and commercial aviation teams can achieve faster repairs, reduce costs, and ensure the long-term reliability of critical aircraft components. Our solutions are designed to extend the fatigue life of parts, minimize corrosion damage, and improve overall fleet readiness.
Explore the possibilities